Innovation as the key
XTEC GmbH
The customer
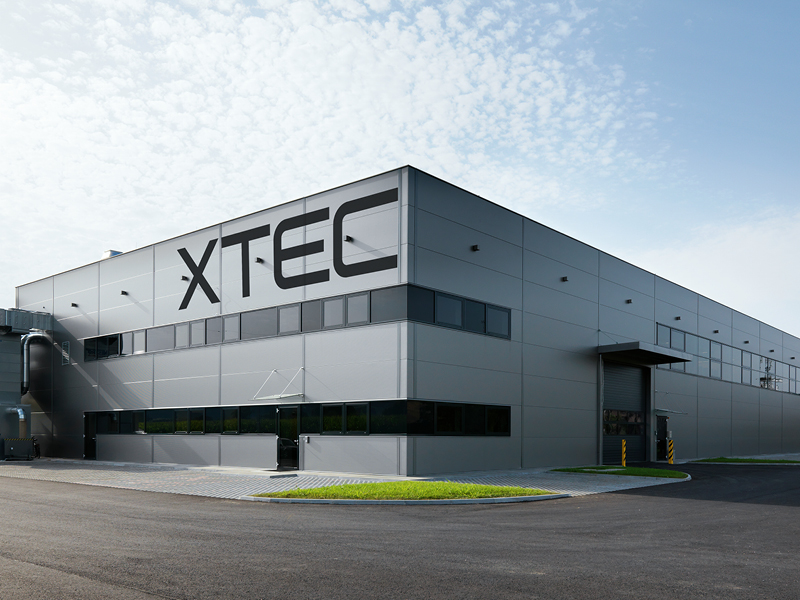
In around 13 years, XTEC has developed into an innovative joinery consisting of 50 young, dedicated technicians and carpenters in St. Margarethen an der Raab, Eastern Styria (Austria). As a project coordinator, the company works with renowned architects, designers and international companies to produce and assemble customised exhibition stands and high-quality furniture worldwide. XTEC realises complete solutions to the highest standards in all areas, supported by state-of-the-art production facilities, development expertise and the most advanced technologies, which enable the well-coordinated team to handle complex projects reliably and successfully worldwide.
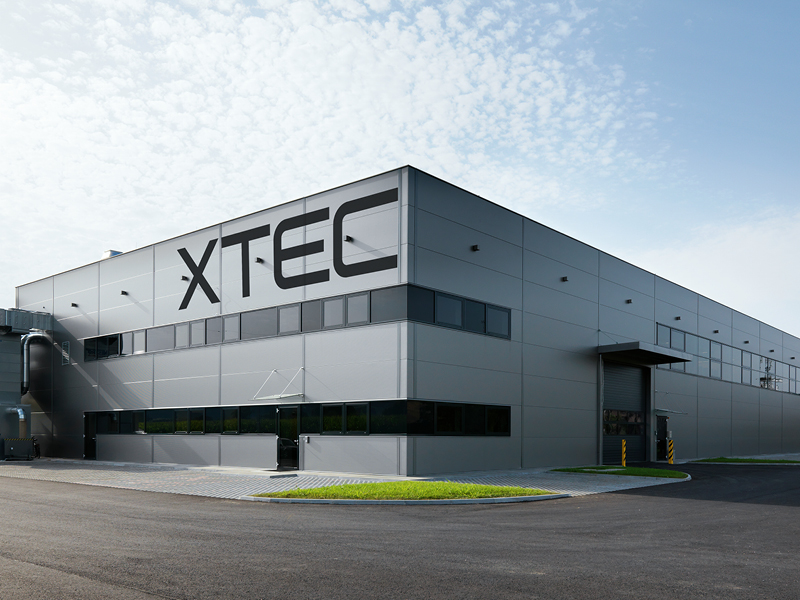
The challenge
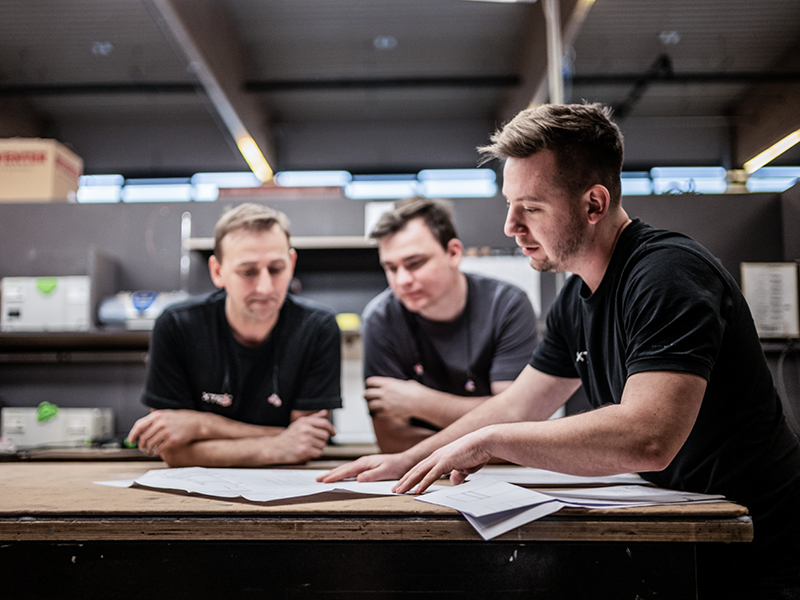
XTEC GmbH combines professional production techniques with excellent project management and the advantages of a furniture manufacturer in its high-tech joinery. The implementation of an ERP system presented major challenges, including the right level of master data, production flexibility, optimised material and resource planning and the integration of machines and joinery software for furniture planning. It was also necessary to integrate a network of suppliers and service providers into the processes in order to ensure transparency, greater flexibility and control options.
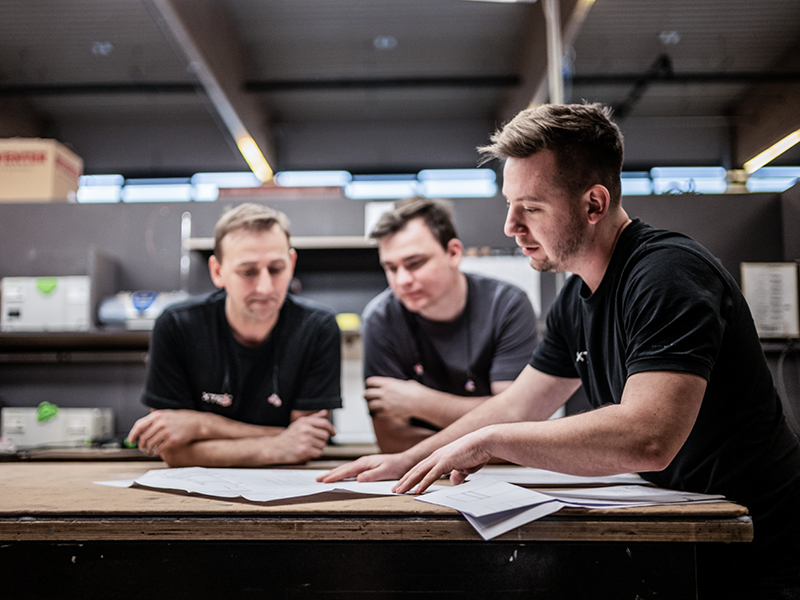
The solution
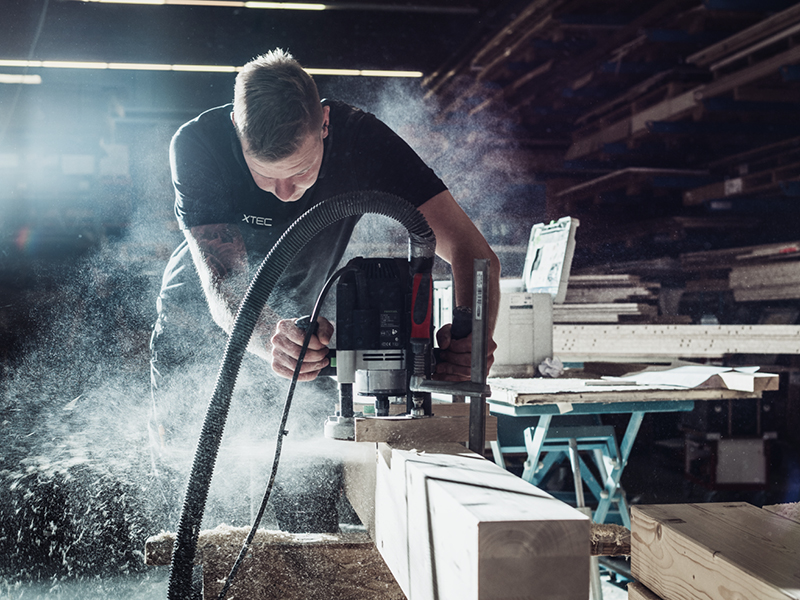
During the project, it became clear that the processes in the company come before the software solution. Customer projects are created in the ERP system and transferred to the planning software via interfaces, where drawings and 3D models are created. Master data from the ERP system enables the return of parts lists and work plans as well as costing. Quotation and order processing, planning and control of production and logistics also take place in the ERP system. The integrated warehouse management system efficiently supports the material flow along the supply chain, especially through the use of mobile scanners.
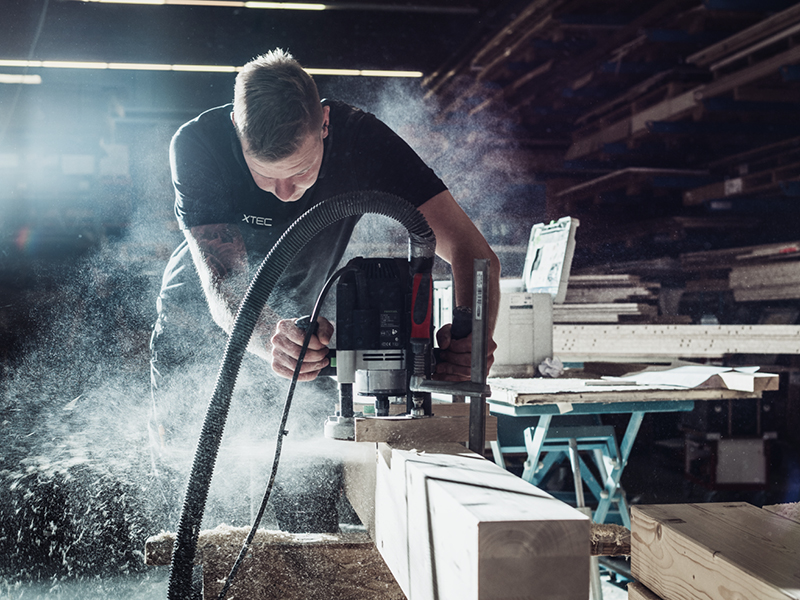
The result
The simple and fast creation of quotations enables smooth conversion into orders and production processes. In addition, transparency and analysability facilitate order planning and control. This makes it possible to provide the customer with qualified and reliable information on the status of their order at any time.
The feedback
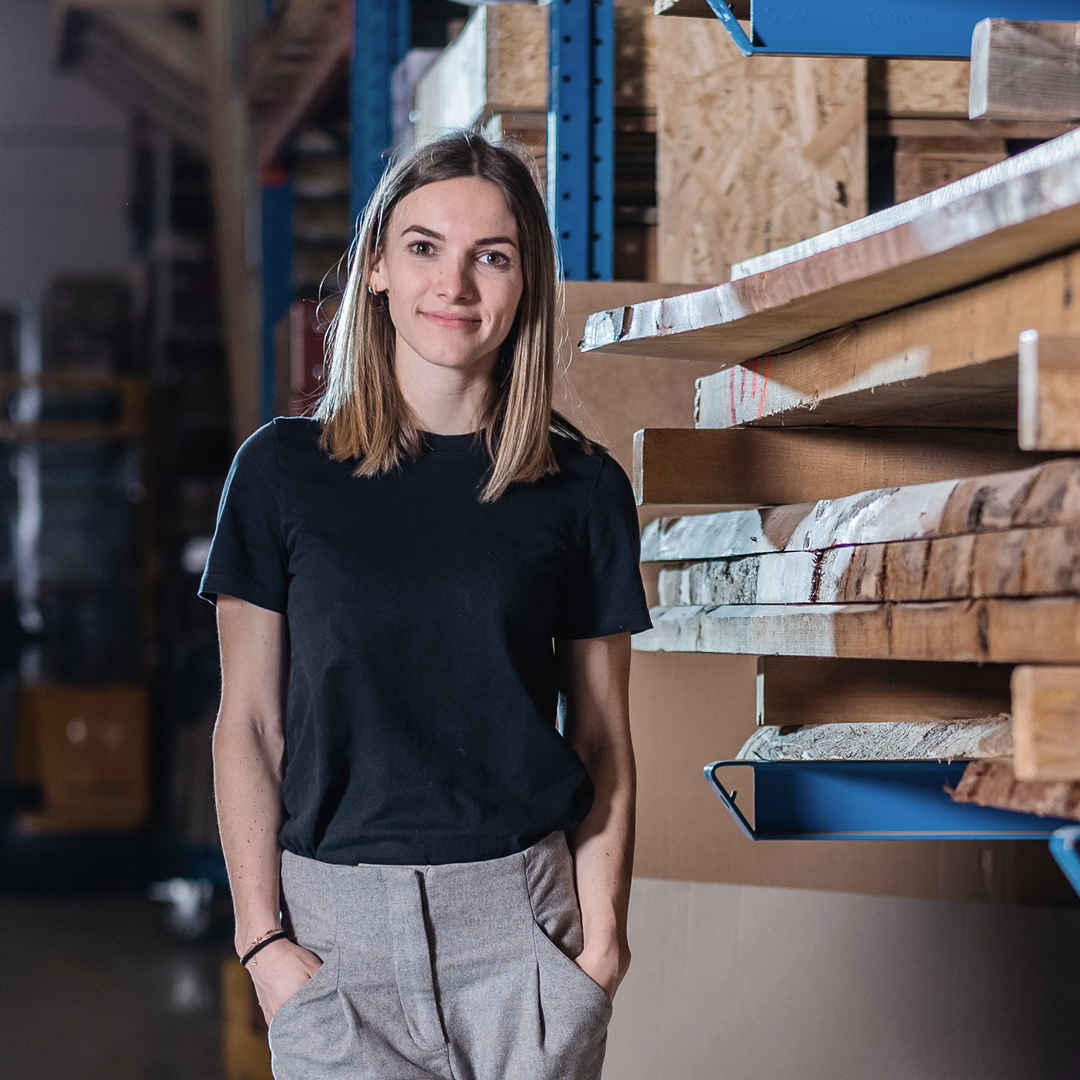
"With the xalax team, we have found a professional partner who has implemented our new ERP system and continues to support it to our complete satisfaction. This has helped us to achieve greater transparency and clear structures in many areas, so that we can now work faster and more efficiently across all systems. Industry 4.0 is already part of our everyday life. Thanks to the changeover, we can now focus even more intensively on design, product quality and new materials."
Fabienne Hierzer, Managing Director XTEC GmbH
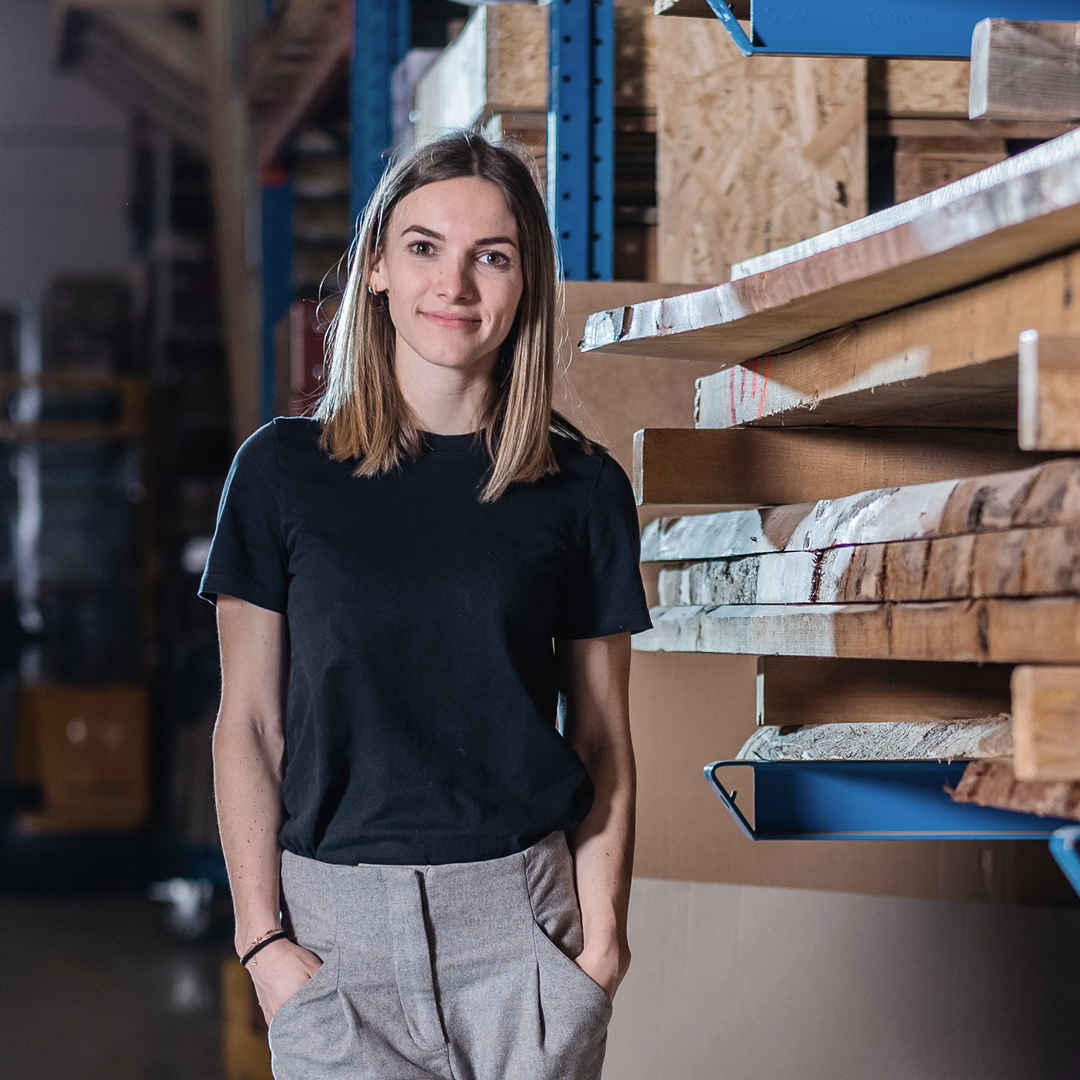